In the realm of electrical engineering and power distribution, the choice of core material for transformers and inductors plays a crucial role in determining the efficiency and performance of the equipment. Two popular choices for core materials are amorphous core and nanocrystalline core, each offering unique properties and advantages. In this article, we will delve into the characteristics of amorphous core and nanocrystalline core, and explore the differences between the two.
What is an Amorphous Core?
An amorphous core is a type of magnetic core material that is characterized by its non-crystalline atomic structure. This unique atomic arrangement gives amorphous cores their distinctive properties, including low core loss, high permeability, and excellent magnetic properties. The most common material used for amorphous cores is an iron-based alloy, typically containing elements such as iron, boron, silicon, and phosphorus.
The non-crystalline nature of amorphous cores results in a random arrangement of atoms, which prevents the formation of magnetic domains and reduces eddy current losses. This makes amorphous cores highly efficient for applications where low energy loss and high magnetic permeability are essential, such as in power distribution transformers and high-frequency inductors.
Amorphous cores are manufactured using a rapid solidification process, where the molten alloy is quenched at a very high rate to prevent the formation of crystalline structures. This process results in an atomic structure that lacks long-range order, giving the material its unique properties.
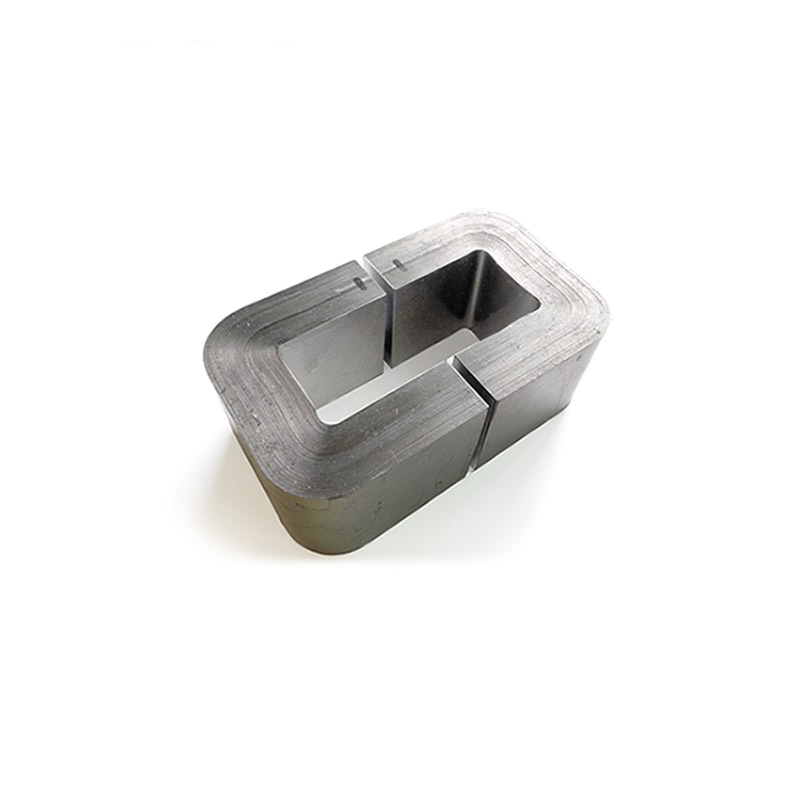
What is a Nanocrystalline Core?
On the other hand, a nanocrystalline core is a type of magnetic core material that consists of nanometer-sized crystalline grains embedded in an amorphous matrix. This dual-phase structure combines the benefits of both crystalline and amorphous materials, resulting in excellent magnetic properties and high saturation flux density.
Nanocrystalline cores are typically made from a combination of iron, nickel, and cobalt, along with small additions of other elements such as copper and molybdenum. The nanocrystalline structure provides high magnetic permeability, low coercivity, and superior thermal stability, making it suitable for high-power applications and high-frequency transformers.
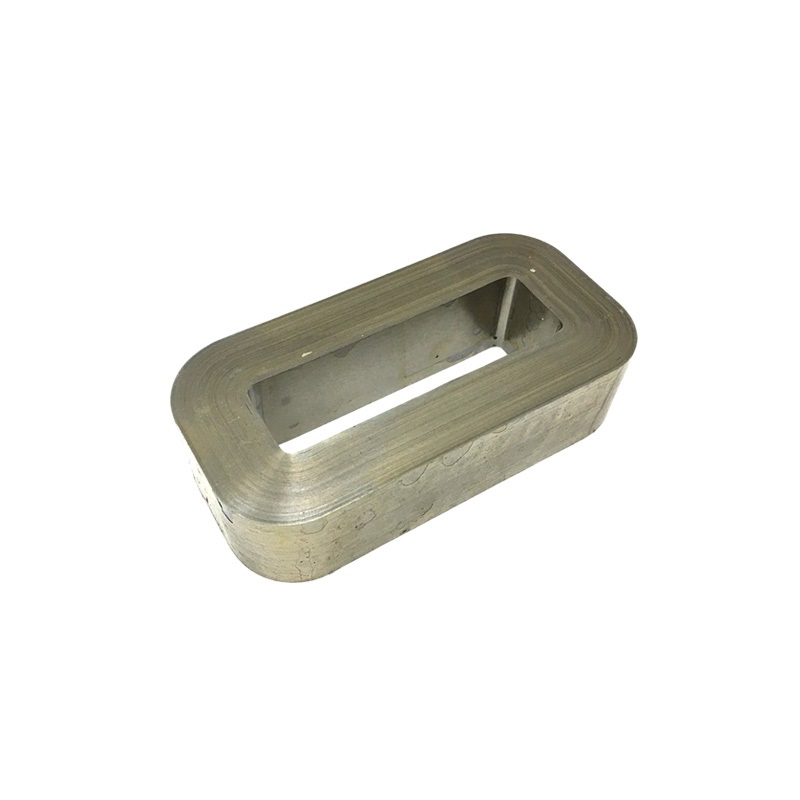
Difference between Amorphous Core and Nanocrystalline Core
The primary difference between amorphous cores and nanocrystalline cores lies in their atomic structure and resulting magnetic properties. While amorphous cores have a completely non-crystalline structure, nanocrystalline cores exhibit a dual-phase structure consisting of nanometer-sized crystalline grains within an amorphous matrix.
In terms of magnetic properties, amorphous cores are known for their low core loss and high permeability, making them ideal for applications where energy efficiency is paramount. On the other hand, nanocrystalline cores offer higher saturation flux density and superior thermal stability, making them suitable for high-power and high-frequency applications.
Another key difference is the manufacturing process. Amorphous cores are produced through rapid solidification, which involves quenching the molten alloy at a high rate to prevent crystalline formation. In contrast, nanocrystalline cores are typically produced through annealing and controlled crystallization of amorphous ribbons, resulting in the formation of nanometer-sized crystalline grains within the material.
Application Considerations
When selecting between amorphous cores and nanocrystalline cores for a specific application, several factors need to be considered. For applications that prioritize low energy loss and high efficiency, such as in power distribution transformers and high-frequency inductors, amorphous cores are often the preferred choice. Their low core loss and high permeability make them well-suited for these applications, contributing to overall energy savings and improved performance.
On the other hand, for applications that require high saturation flux density, superior thermal stability, and high-power handling capabilities, nanocrystalline cores are more suitable. These properties make nanocrystalline cores ideal for high-power transformers, inverter applications, and high-frequency power supplies, where the ability to handle high magnetic flux densities and maintain stability under varying operating conditions is crucial.
In conclusion, both amorphous cores and nanocrystalline cores offer unique advantages and are tailored to specific application requirements. Understanding the differences in their atomic structure, magnetic properties, and manufacturing processes is essential for making informed decisions when selecting core materials for transformers and inductors. By leveraging the distinct characteristics of each material, engineers and designers can optimize the performance and efficiency of their power distribution and conversion systems, ultimately contributing to advancements in energy efficiency and sustainable power technologies.
Post time: Apr-03-2024